GeneticSharp in the Wild: Simulation-based layout optimization for multi-station assembly lines
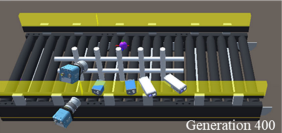
I started a series of posts about some outstanding scientific papers and projects using GeneticSharp.
For this sixth post the chosen one is the Simulation-based layout optimization for multi-station assembly lines
.
Introduction
Presents a novel approach for the automated 3D-layout planning of multi-station assembly lines. The planning method is based on a comprehensive model of the used production resources, including their geometry, kinematic properties, and general characteristics. Different resource types can be included in the planning system. A genetic algorithm generates and optimizes possible layouts for a line.
Usage
The optimization aims to minimize the line’s area and the costs for assembling the line while simultaneously optimizing the resources’ positioning to perform their tasks. The line’s cycle time is considered as a boundary condition. For the evaluation of different layout alternatives, a multi-body simulation is performed. A parameter study is used to set the algorithm’s parameters. Afterward, the algorithm is applied to three increasingly complex examples to validate and evaluate its functionality. The approach is promising for industrial applications as it allows the integration of various resource types and individualization of the optimization function.
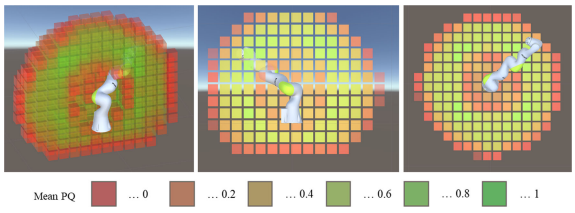
Examples for the evaluation of positions in the workspace of an LBR iiwa 7 robot
Results
The presented system is highly flexible and supports the positioning of multiple resource types. It is also open to integrating more resource variants or customizing the fitness function to reflect the individual user’s preferences accurately. The integration of more resource models and the modeling of more resource types would be the logical next step to improve the system further.
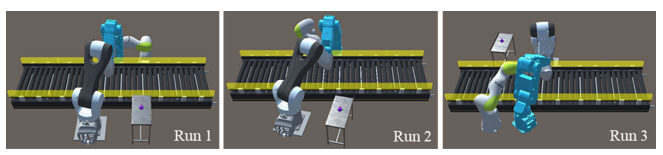
The final layout of the first three runs of the first example
Authors
Daria Leiber, David Eickholt, Anh-Tu Vuong, and Gunther Reinhart wrote the paper for Department of Mechanical Engineering, Institute for Machine Tools and Industrial Management, Technical University of Munich, Germany.
Further reading
You can access the full paper directly at Journal of Intelligent Manufacturing.